Getting Started:
Here Ampericon will list the equipment, instructions and prompts found with regards to the Graphene Battery.
Test Protocol Steps
1. Charge the Graphene Battery to 58V
- Switch the Graphene Battery and your Inverter to ON
- Make sure your rectifier is set to 100A
- As the Graphene Battery Charges periodically check the charge with your Voltmeter and the BMS system
- The voltmeters cables should be placed positive to positive and negative to negative (full is 58V)
- To check the Pack Voltage on the BMS system, hit MENU then select ANALOG INFO view PackV, Pack Voltage is full when it displays 58V
2. Discharging the Graphene Battery to 40V
- Switch the Graphene Battery and your Inverter to ON
- Make sure your rectifier is set to 100A
- As the Graphene Battery Discharges periodically check the charge with your Voltmeter and the BMS system
- The voltmeters cables should be placed positive to positive and negative to negative (lowest allowed is 40V)
- To check the Pack Voltage on the BMS system, hit MENU then select ANALOG INFO view PackV, Pack Voltage is fully discharged when it displays 40V
3. Ensuring Graphene Battery Pack temperature does not rise by more than < 6° C at 100 A charge rate
- Switch the Graphene Battery and your Inverter to ON
- Make sure your rectifier is set to 100A
- As the Graphene Battery Charges periodically check the battery’s temperature with your Power Analyzer and the BMS system
- To check the Graphene Battery’s temperature changes, hit MENU then select ANALOG INFO then while on that page hit TEMPERATURE. Here you will see T1, T2, T3, and T4 with temperature readings in Celsius for each.
- Keep the BMS LCD on the Temperature page and make sure that it does not rise more than < 6° C during the charge process.
4. Full Charge (58 V) reached ~ 35 min. @ 100A charge (Initial voltage 40V)
- Follow the steps found in Step 2 to discharge fully to 40V
- Then follow the steps found in Step 1 to start charging again, use your stopwatch or smartphone to ensure that a full charge only takes around 35 min.
5. Full Discharge (40 V) reached ~ 55 min. @ 50A load (Initial voltage 58V)
- After completing Step 4 simply set your rectifier at 50A
- Then discharge the battery 100% to 40V, use a smartphone or stopwatch to keep time, and that the process takes the desired amount of time (55min.)
6. Ensuring Graphene Battery Pack temperature does not rise by more than < 10° C at 100 A charge rate (1 C rate of charge)
- Switch the Graphene Battery and your Inverter to ON
- Make sure your rectifier is set to 100A
- As the Graphene Battery Charges periodically check the battery’s temperature with your Power Analyzer and the BMS system
- To check the Graphene Battery’s temperature changes, hit MENU then select ANALOG INFO then while on that page hit TEMPERATURE. Here you will see T1, T2, T3, and T4 with temperature readings in Celsius for each.
- Keep the BMS LCD on the Temperature page and make sure that it does not rise more than < 10° C during the charge process.
7. Voltage steady (within 1V) @ 20ΩA load for 55s (Starting voltage 58V)
- Connect the Immersion Heat Rod to your rectifier through its AC port with the Graphene Battery connected to it.
- Use your Voltmeter or view the Pack Voltage via the BMS to view any changes in voltage (fluctuations can be viewed with the Power Analyzer if you notice any strange readings initially)
- Set your timer to a 55s countdown and confirm steady voltage during the allotted time
8. Operation Pro-Rated @ 45° C (w/ 20Ω load < ±1V drop in 20s)
- Conduct the same test from Step 7 with the room temperature set to 45° C.
BMS Error Indicators
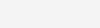
Test Objectives Summary:
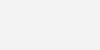
Exceptions
- If the Batteries go into SCP (Red LED light) or Short Circuit Protection. Turn off batteries
- Discharge residual charge on battery terminals
- Startup using Turn On procedure described above
- If Error Persists:
- Turn off batteries
- Turn off battery disconnect
- Discharge residual voltage on terminals
- Charge the batteries briefly with a small boost charger @ 48 V
- This will resolve the SCP condition within a few minutes
- Follow Turn On steps described above
1st installation phase
- All Super Cap’s must be connected correctly
- Positive wires hook up to positive connectors, negative wires to negative connectors
- Hook up 1st Super Cap (herein referred to as Master) to the inverter charger at both positive and negative ports
- Use the provided ethernet cables and first connect it the Master’s “COMM” outlet, your 1st additional battery (now referred to as Slaves) and connect this 1st ethernet cable into the “CONNECTOR” outlet.
- Each subsequent Super Cap should be connected to one another in the same fashion; Slave 1 COMM connects to Slave 2 CONNECTOR, Slave 2 COMM connects to Slave 3 CONNECTOR and so on.
- Naturally, each Super Cap that has been connected in this fashion with their ethernet cables.
- Each Super Cap should also have their positive and negative outlets connected so that for example Master + and Slave 1 + are connected, Master – and Slave 1 – connected then Slave 1 + and – are to Slave 2 + and – respectively and so on until all slaves are connected in this manner. Positive to Positive and Negative to Negative.
- Once all wiring has been completed, it is time to set the Master’s and respective slaves’ dip switches in order for it to communicate properly between the Inverter Charger and Super Caps’ Battery Management Systems (BMS) here you can see how the dip switches are set when only one Super Cap is being used, see the next section’s table for setting multiple Super Caps in parallel.
- Now that everything is properly connected and settings double checked, make sure the inverter your parallel connected battery set is connected to is sending out a maximum charge voltage of 58.8V/DC.
- This methodology is the same for discharging the Super Cap as well, you will know when the discharge cutoff point has been reached when the Super Cap reading is at 42V/DC
Single power box

Multiple power box in parallel
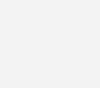